Electric Supercharger, round three...
Posted: Sun Jun 03, 2007 8:42 am
Before I start yes I know they're shit, and yes I know they don't do anything. Well, do they?
OK, after doing months and months of research (it all began last October but I kept it quiet) I have finally got a concept for one that WILL work and WILL produce boost.
It all began when TomOTEC and I bought some plans from the net. We didnt like the look of them because it was all a bit ghetto, and the fact you needed 3 car batteries wasnt that appealing either. And, at the end of it all you would end up with a pretty weak boost anyways.
However, in the months afterwards I *did* find one that provides a nice boost. Problem was it was $2000 lol.
Basically it's a centrifugal but powered by electricity. And it looks just like the front end of a turbo (minus the exhaust housing and wastegate.)
So I went on ebay and bought one of the plastic bilge pumps to give me an insight into what goes on, ended up blowing it up with 40 volts. It wouldnt have worked (and I knew this) because it was made from plastic and concaved when any pressure built. I did have fun blowing things accross the living room until a really bad burning smell came from the motor.. It was $25, the guy selling them only does so to stop people getting ripped off..
Anyway, time to bring you all up to speed. I decided a long time ago that I was going to see this through, and I was going to end up with something that could be ran electrically and pump air into my intake system. I have seen this being done with a leaf blower and it works. I dont want to argue over that, it was Dyno'd and proven.
Now this isnt going to be something anyone can run out and do, remember Im 33 years old and have a EXTREMELY technical background. If I dont know how something works I will get one and spend the day taking it apart to figure it out. By the end of the day I know *EXACTLY* what it does.
So I had put my project to one side recently because of everything else I have been doing on the car, but I still had all kinds of shit laying around my apartment ready for the project to kick back into action.
And then yesterday I got the call that has re-ignited the whole affair.. My friend Ryan (with the rather stupidly fast STI wagon) called me and said "dude, I got you a turbo to play with, come and get it"
Before anyone plays judge, jury and executioner remember this turbo was spent. All of the bearings had died and there was play in the impellor shaft. Using it as intended would have ended in tears. BUT.. It was all complete and therefore perfect because I didnt need any of that anyways.
So I got over to Ryan's yesterday and began learning what goes into a turbo, what it does and how it works.. Ryan said that they operate around the 25k-30k RPM range and provide a real strong boost there. So we set to taking it apart..
Before we did that however we rigged a 15,000 RPM angle grinder to the exhaust impellor and wound the turbo up. Nice boost of air circulating the garagge LMAO. (P.S DONT try this at home. Even the dust from the garage floor almost took skin of my legs.. We're talking danger here).
So now I knew what I was going to use for the 'motor'.. I have a grinder that produces 18k RPM that I bought to cut my seat brackets... It was $35 and has sat in the box since then. I'm no metalworker...
However, I can already hear the skeptics among us saying "dude, 18k RPM isnt enough" and they're absolutely right. And that's where my skill comes in...
The concept.
I have an immaculate turbo. All that was done on it were the internal bearings. The housing, impellor and parts I need for this are all there.
I also have an angle grinder motor, capable of 18k RPM.
Now, to make this bastard REALLY give off boost Im going to need to double the RPM output of that motor.. How? easy.
I have a back wheel from a mountain bike over @ my uncles, with a good chain. Bike was destroyed when I ran into a ditch and bent the front end, but it has what I need..
So here is what will sit on the back of the now modded turbo -
It's a steel plate with spindles on rollerskate bearings.. (well at the moment its a pic I made in paint). I studied ratios in school and I will be running 2:1. The drive gear will be twice the size of the gear on the spline of the turbo, making me spin around the 36000 RPM mark. And angle grinder motors are INCREDIBLY torquey too, theyre made to cut steel.
So the small gear will go down into the turbo, and the large gear will be on the grinder motor. And the red in the pic is a MTB chain.
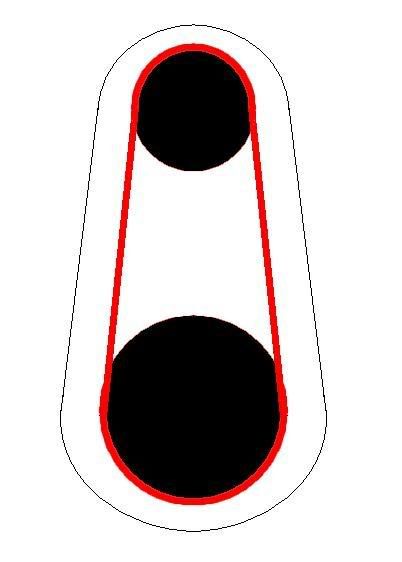
And now for what I have to do with the turbo.
This is the ass end of the rear assembly (Turbo is in 2 halves held together with a large spring clip.. This turbo comes from a MITSU)
The hole in the middle will be skimmed out to hold a rear bearing (also in the pic)

There is a nice lip inside that will stop the bearing from falling in.
And now how the frontal bearing will be held in..
Here is the front end of the rear part of the turbo -
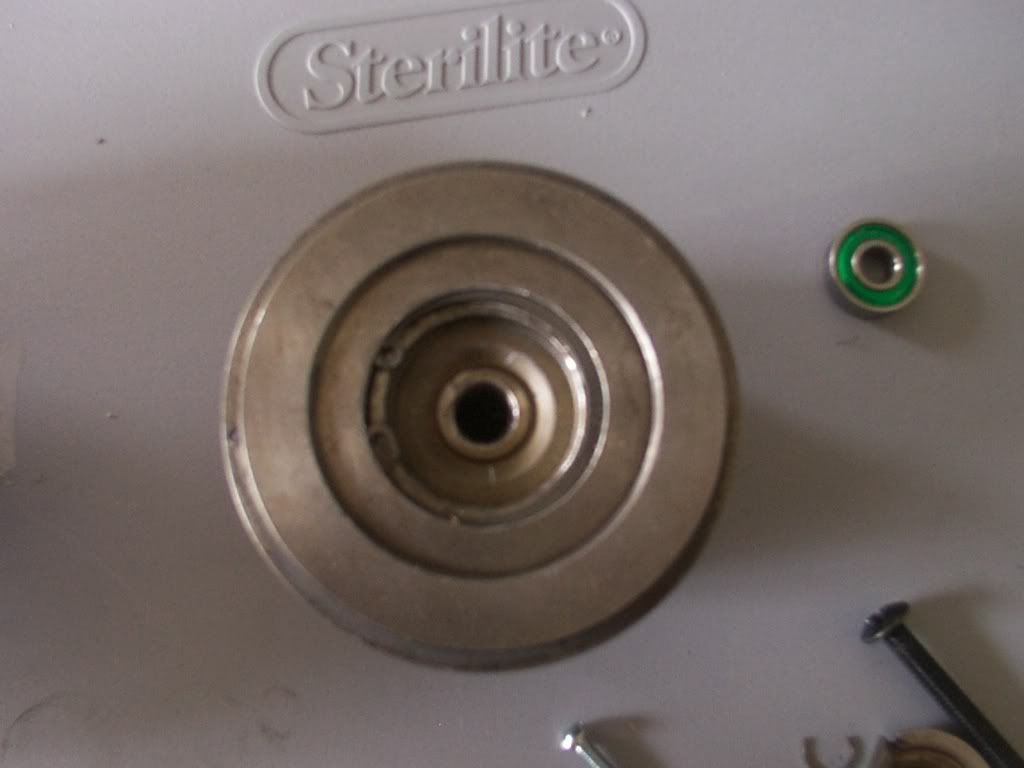
And here is what I will be getting machined.. A bearing cup to hold said frontal bearing.
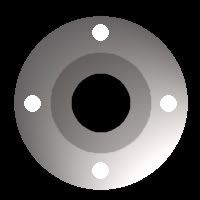
And wehre it sits. 4 holes hold countersunk allen bolts holding it in, bearings press into center..
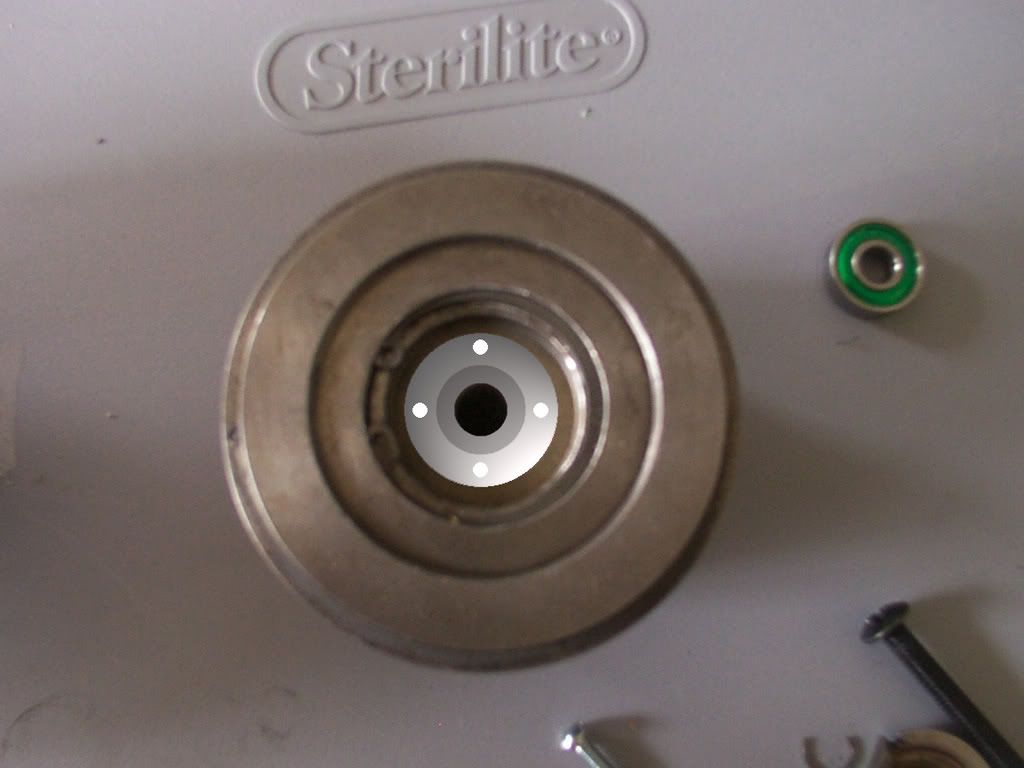
Here is the worn and snapped spline from the old assembly -
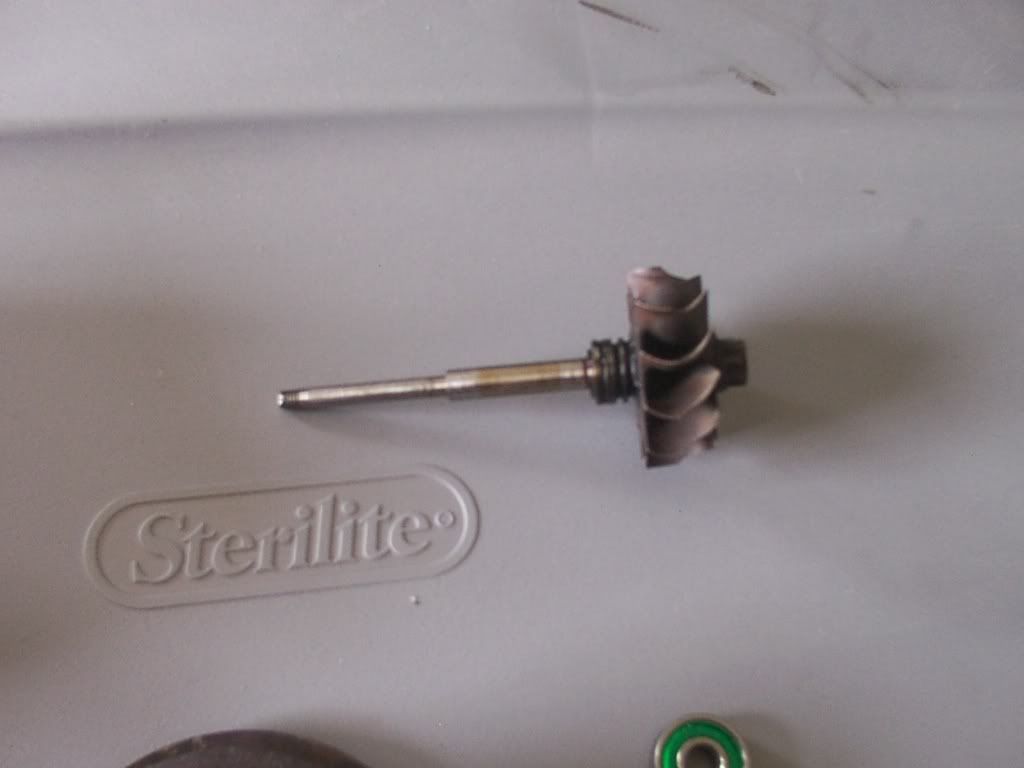
I will be getting one machined that fits snug into the rollerskate bearings (which are ceramic BTW, donated by the same guy who gave me the turbo) At the back end it will protrude out and be welded to the small gear. Front end it will taper in and the impellor will bolt on. It will ride snug inside the bearings, and spin really smooth.
The impellor. This turbo is really well machined.. The diffuser is part of the body.. Thankfully the impellor isnt damaged and pretty much like brand new
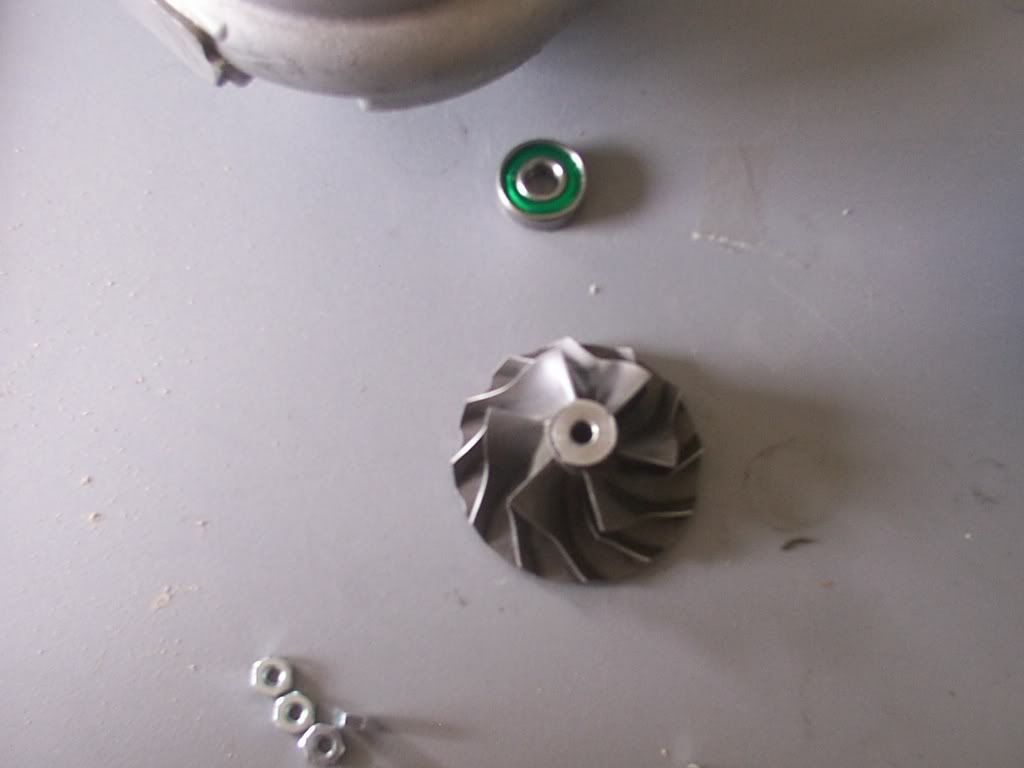
Top end of turbo -
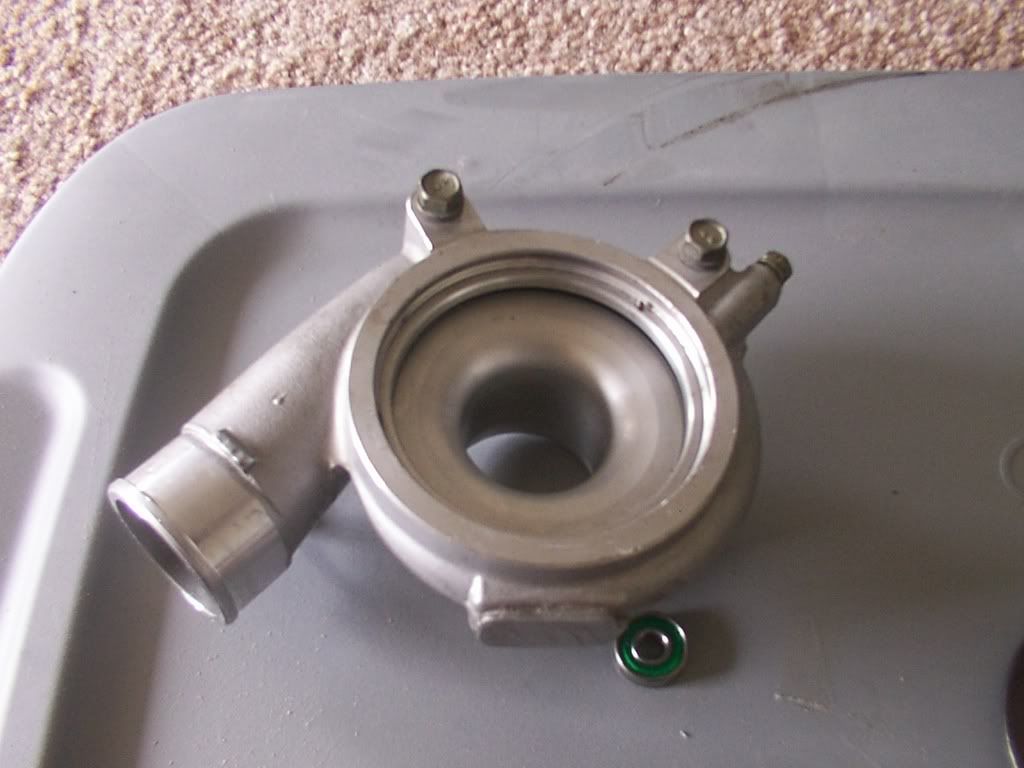
Where the impellor rides, 1.5 mm off this housing..
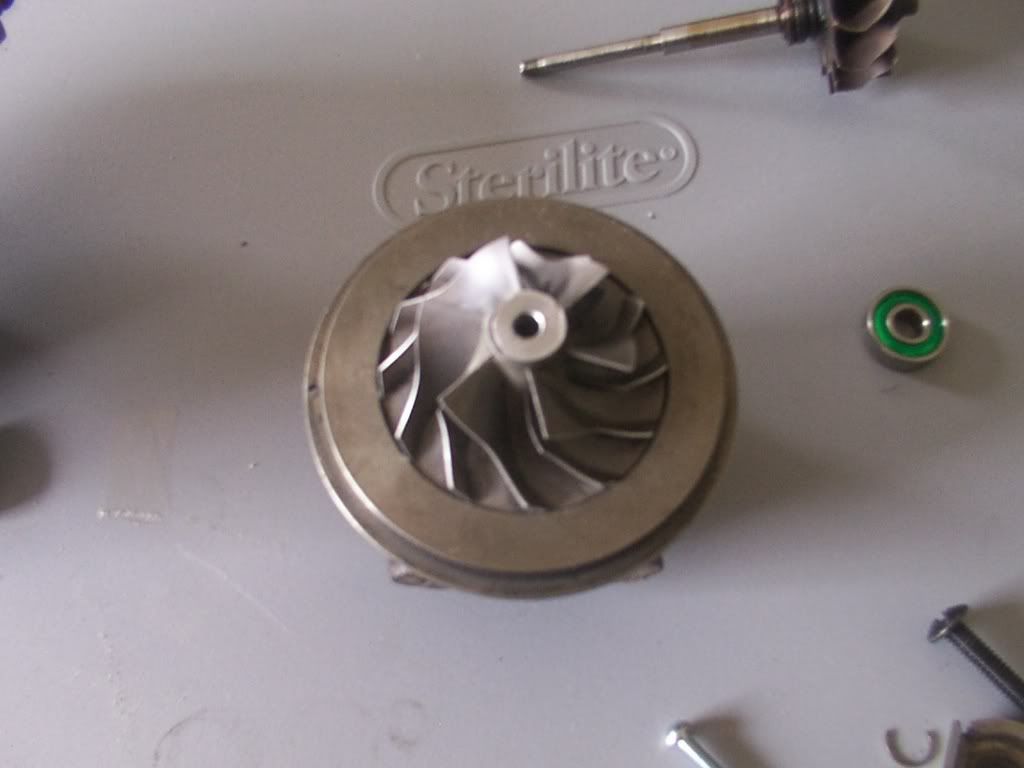
And what it looks like when assembled -
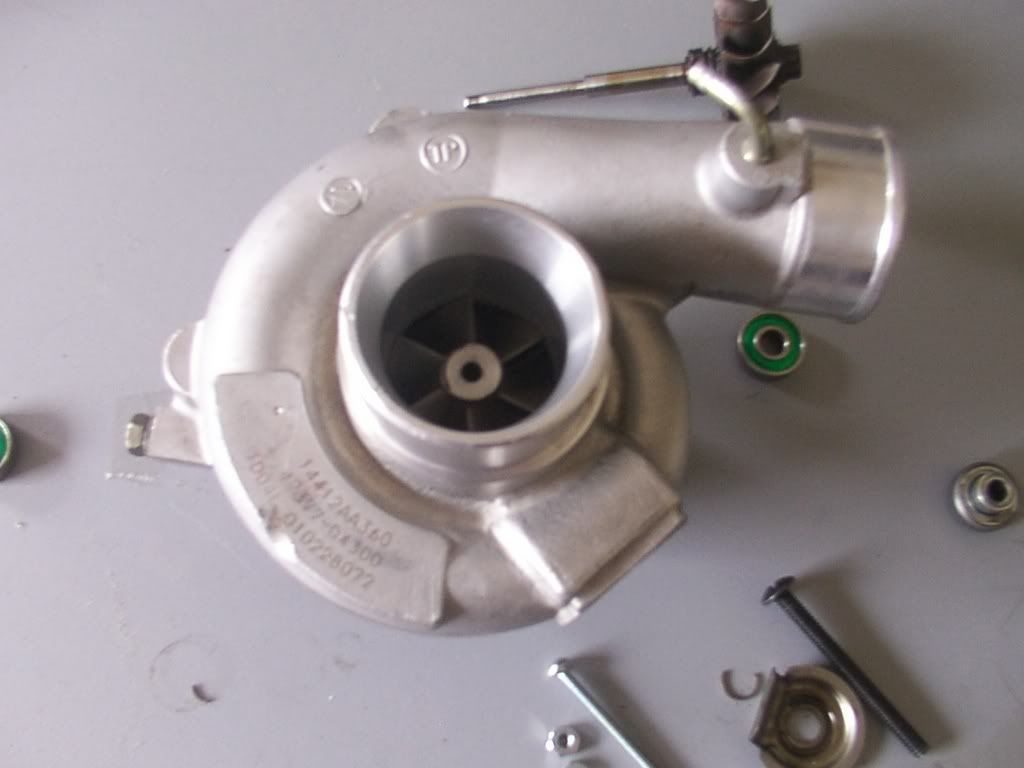
Fabrication has begun and is going well, here is a part of the bracket assembly that will hold the gear/chain/motor assembly onto thr back of the tuebo, basically making it a centrifugal air pump.
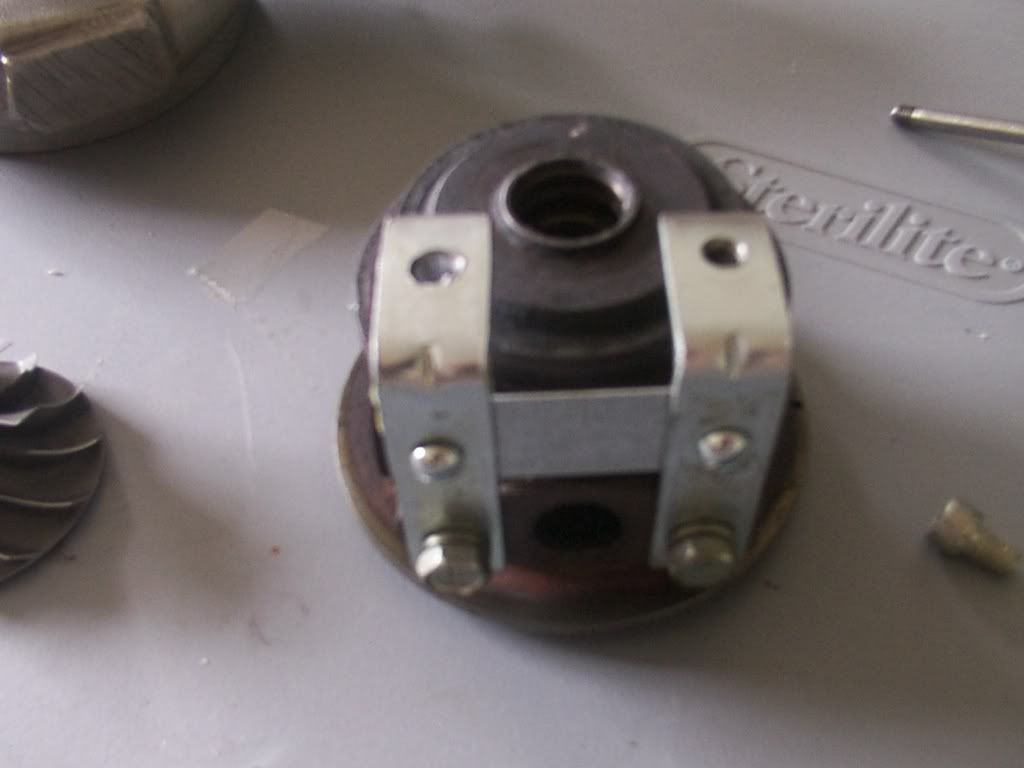
And I'll be off to the machine shop soon to get all the parts I need planned out and machined.
I will, of course, keep everyone updated
*Note* I wasnt entirely truthful about the whole thing as I would have gotten into shit with the moderators on the forum I visit. However, this bastard will work !
OK, after doing months and months of research (it all began last October but I kept it quiet) I have finally got a concept for one that WILL work and WILL produce boost.
It all began when TomOTEC and I bought some plans from the net. We didnt like the look of them because it was all a bit ghetto, and the fact you needed 3 car batteries wasnt that appealing either. And, at the end of it all you would end up with a pretty weak boost anyways.
However, in the months afterwards I *did* find one that provides a nice boost. Problem was it was $2000 lol.
Basically it's a centrifugal but powered by electricity. And it looks just like the front end of a turbo (minus the exhaust housing and wastegate.)
So I went on ebay and bought one of the plastic bilge pumps to give me an insight into what goes on, ended up blowing it up with 40 volts. It wouldnt have worked (and I knew this) because it was made from plastic and concaved when any pressure built. I did have fun blowing things accross the living room until a really bad burning smell came from the motor.. It was $25, the guy selling them only does so to stop people getting ripped off..
Anyway, time to bring you all up to speed. I decided a long time ago that I was going to see this through, and I was going to end up with something that could be ran electrically and pump air into my intake system. I have seen this being done with a leaf blower and it works. I dont want to argue over that, it was Dyno'd and proven.
Now this isnt going to be something anyone can run out and do, remember Im 33 years old and have a EXTREMELY technical background. If I dont know how something works I will get one and spend the day taking it apart to figure it out. By the end of the day I know *EXACTLY* what it does.
So I had put my project to one side recently because of everything else I have been doing on the car, but I still had all kinds of shit laying around my apartment ready for the project to kick back into action.
And then yesterday I got the call that has re-ignited the whole affair.. My friend Ryan (with the rather stupidly fast STI wagon) called me and said "dude, I got you a turbo to play with, come and get it"
Before anyone plays judge, jury and executioner remember this turbo was spent. All of the bearings had died and there was play in the impellor shaft. Using it as intended would have ended in tears. BUT.. It was all complete and therefore perfect because I didnt need any of that anyways.
So I got over to Ryan's yesterday and began learning what goes into a turbo, what it does and how it works.. Ryan said that they operate around the 25k-30k RPM range and provide a real strong boost there. So we set to taking it apart..
Before we did that however we rigged a 15,000 RPM angle grinder to the exhaust impellor and wound the turbo up. Nice boost of air circulating the garagge LMAO. (P.S DONT try this at home. Even the dust from the garage floor almost took skin of my legs.. We're talking danger here).
So now I knew what I was going to use for the 'motor'.. I have a grinder that produces 18k RPM that I bought to cut my seat brackets... It was $35 and has sat in the box since then. I'm no metalworker...
However, I can already hear the skeptics among us saying "dude, 18k RPM isnt enough" and they're absolutely right. And that's where my skill comes in...
The concept.
I have an immaculate turbo. All that was done on it were the internal bearings. The housing, impellor and parts I need for this are all there.
I also have an angle grinder motor, capable of 18k RPM.
Now, to make this bastard REALLY give off boost Im going to need to double the RPM output of that motor.. How? easy.
I have a back wheel from a mountain bike over @ my uncles, with a good chain. Bike was destroyed when I ran into a ditch and bent the front end, but it has what I need..
So here is what will sit on the back of the now modded turbo -
It's a steel plate with spindles on rollerskate bearings.. (well at the moment its a pic I made in paint). I studied ratios in school and I will be running 2:1. The drive gear will be twice the size of the gear on the spline of the turbo, making me spin around the 36000 RPM mark. And angle grinder motors are INCREDIBLY torquey too, theyre made to cut steel.
So the small gear will go down into the turbo, and the large gear will be on the grinder motor. And the red in the pic is a MTB chain.
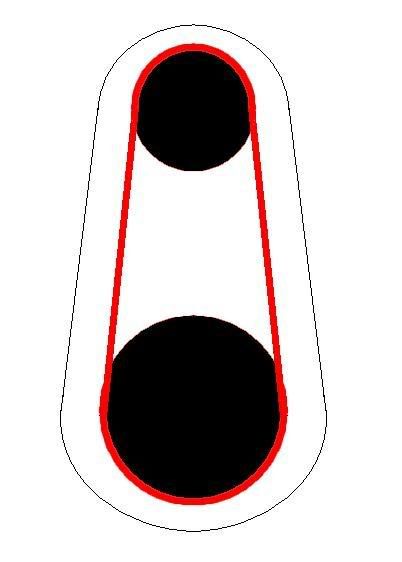
And now for what I have to do with the turbo.
This is the ass end of the rear assembly (Turbo is in 2 halves held together with a large spring clip.. This turbo comes from a MITSU)
The hole in the middle will be skimmed out to hold a rear bearing (also in the pic)

There is a nice lip inside that will stop the bearing from falling in.
And now how the frontal bearing will be held in..
Here is the front end of the rear part of the turbo -
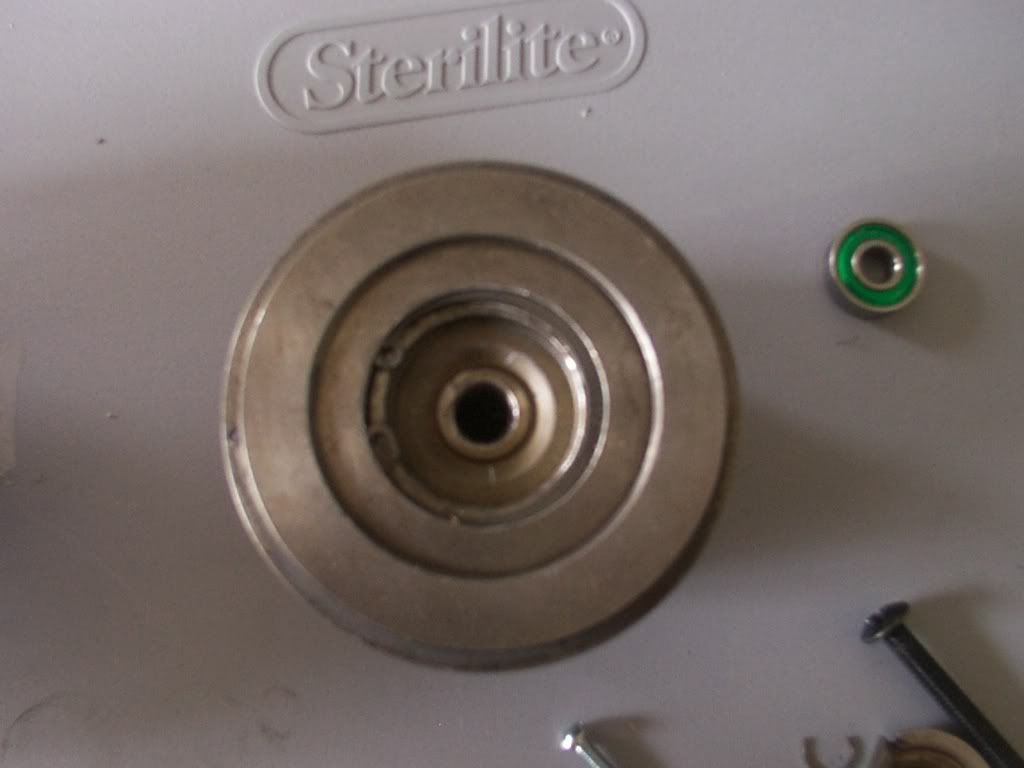
And here is what I will be getting machined.. A bearing cup to hold said frontal bearing.
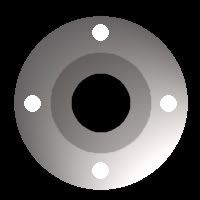
And wehre it sits. 4 holes hold countersunk allen bolts holding it in, bearings press into center..
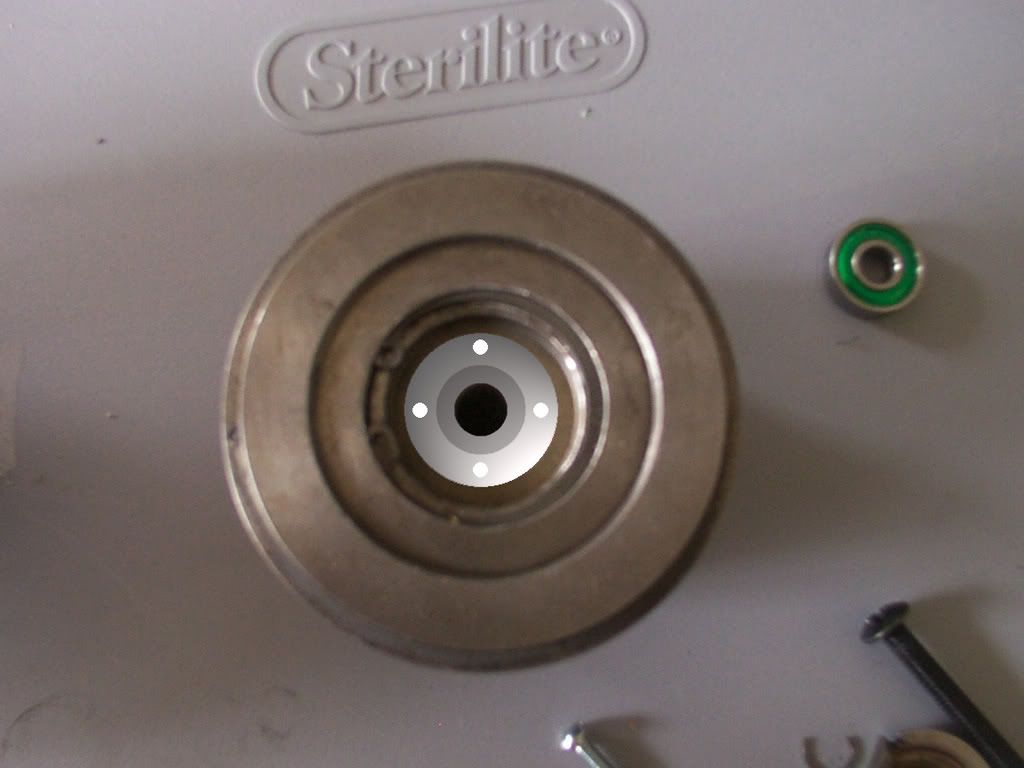
Here is the worn and snapped spline from the old assembly -
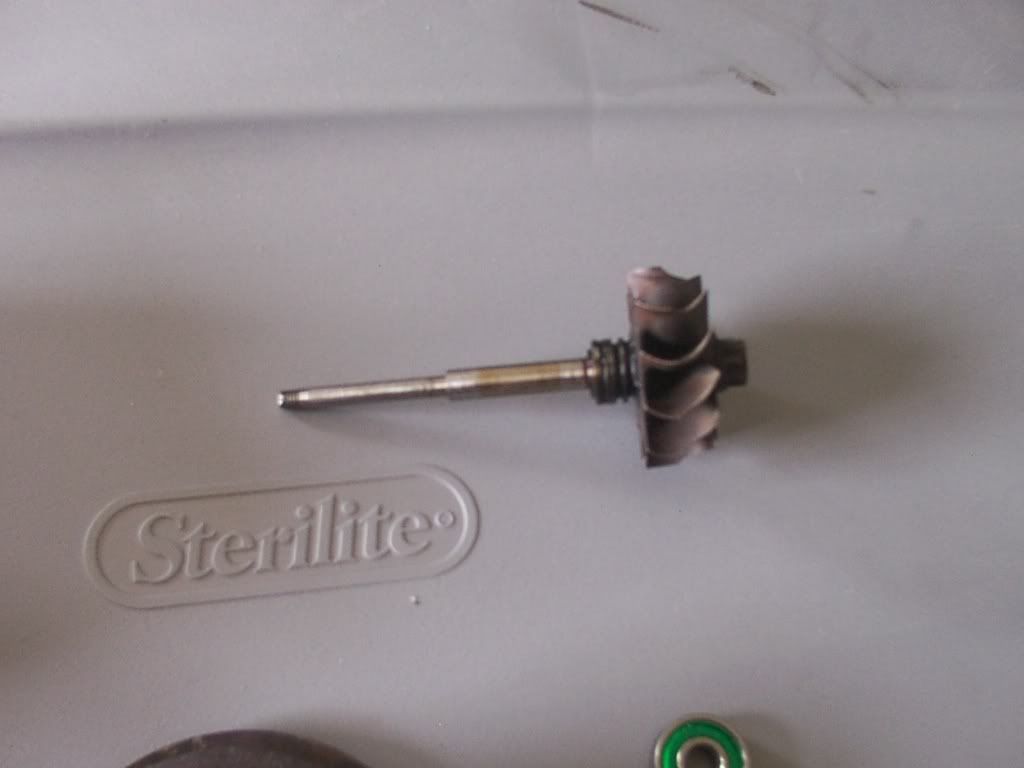
I will be getting one machined that fits snug into the rollerskate bearings (which are ceramic BTW, donated by the same guy who gave me the turbo) At the back end it will protrude out and be welded to the small gear. Front end it will taper in and the impellor will bolt on. It will ride snug inside the bearings, and spin really smooth.
The impellor. This turbo is really well machined.. The diffuser is part of the body.. Thankfully the impellor isnt damaged and pretty much like brand new
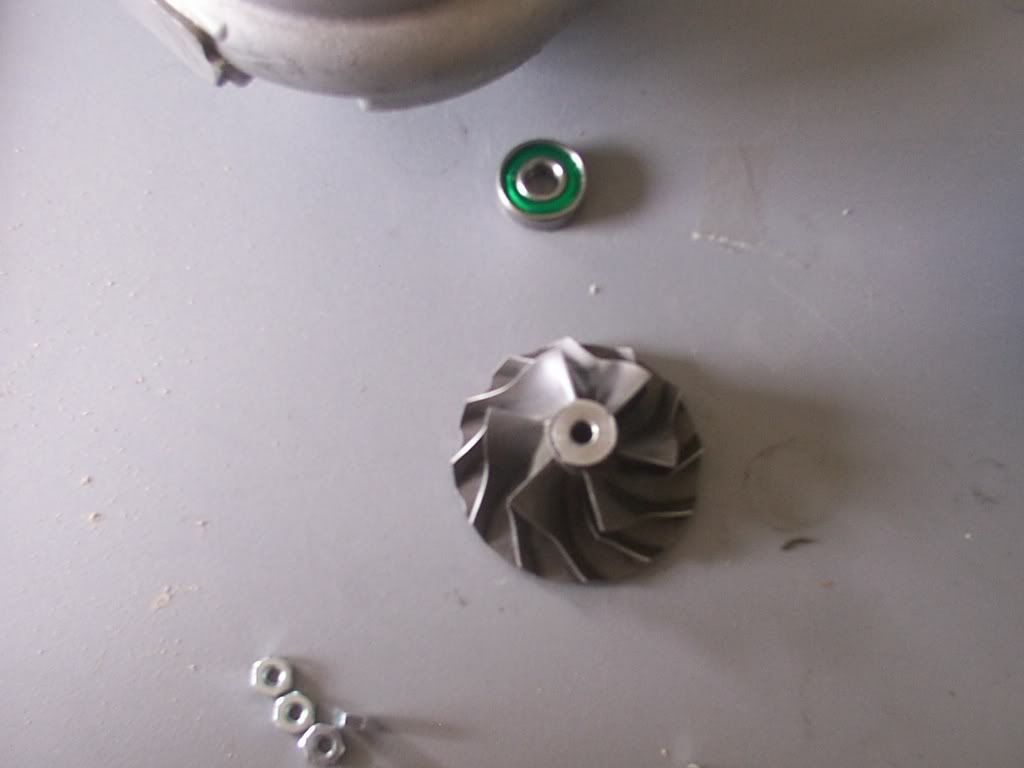
Top end of turbo -
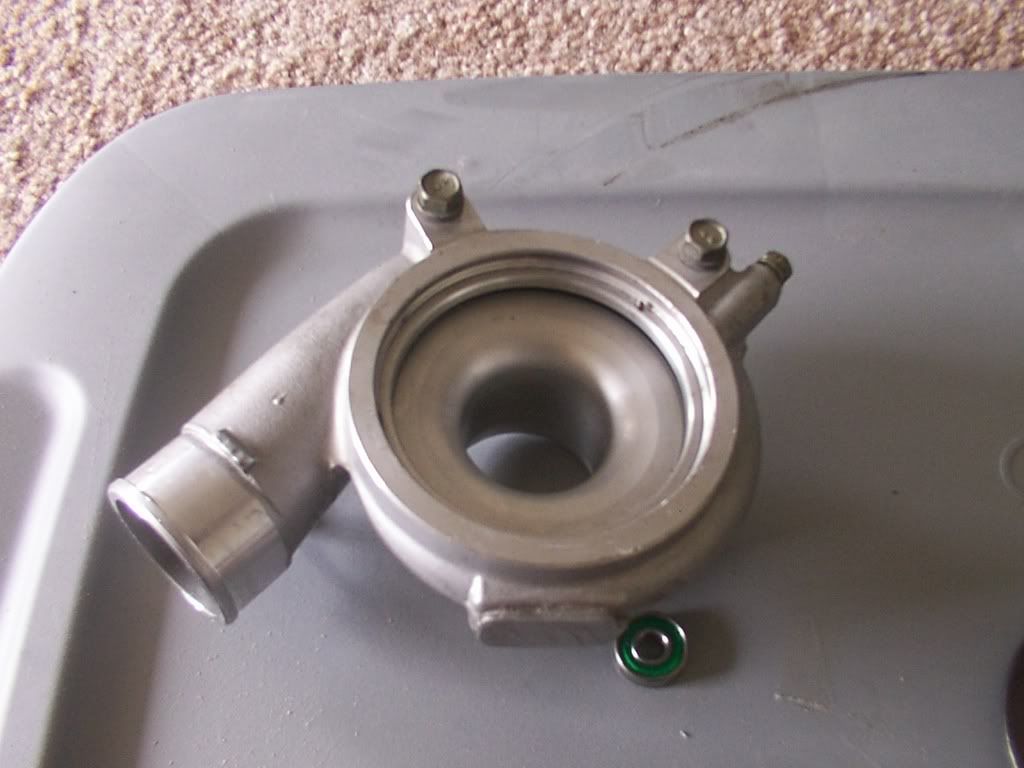
Where the impellor rides, 1.5 mm off this housing..
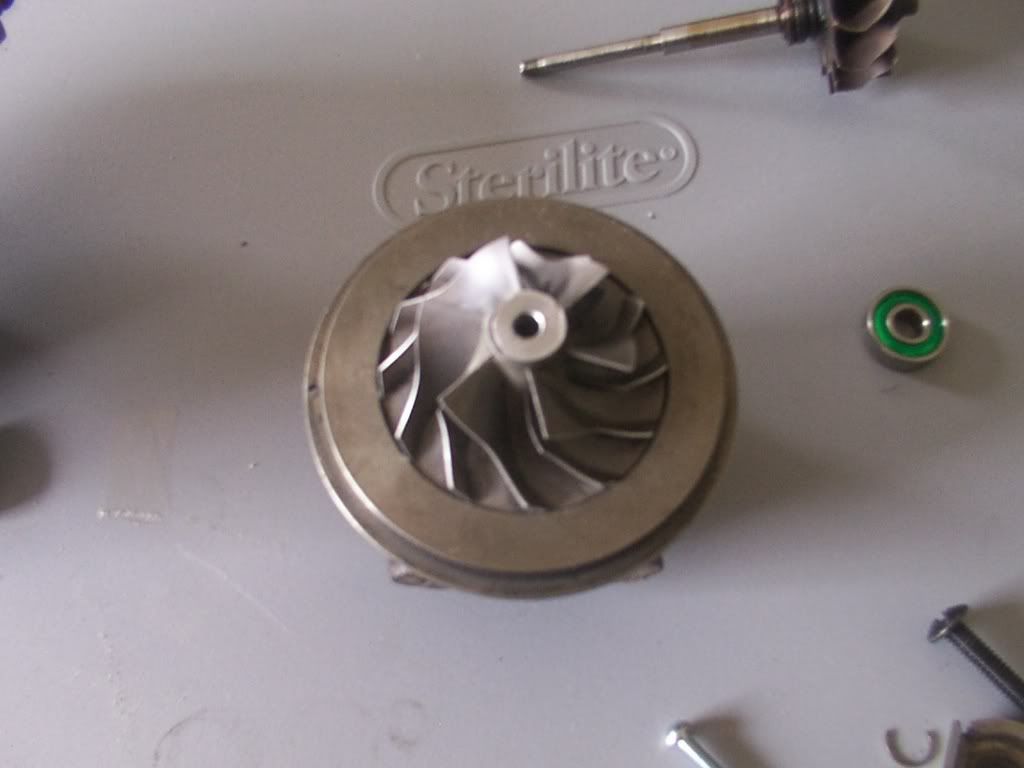
And what it looks like when assembled -
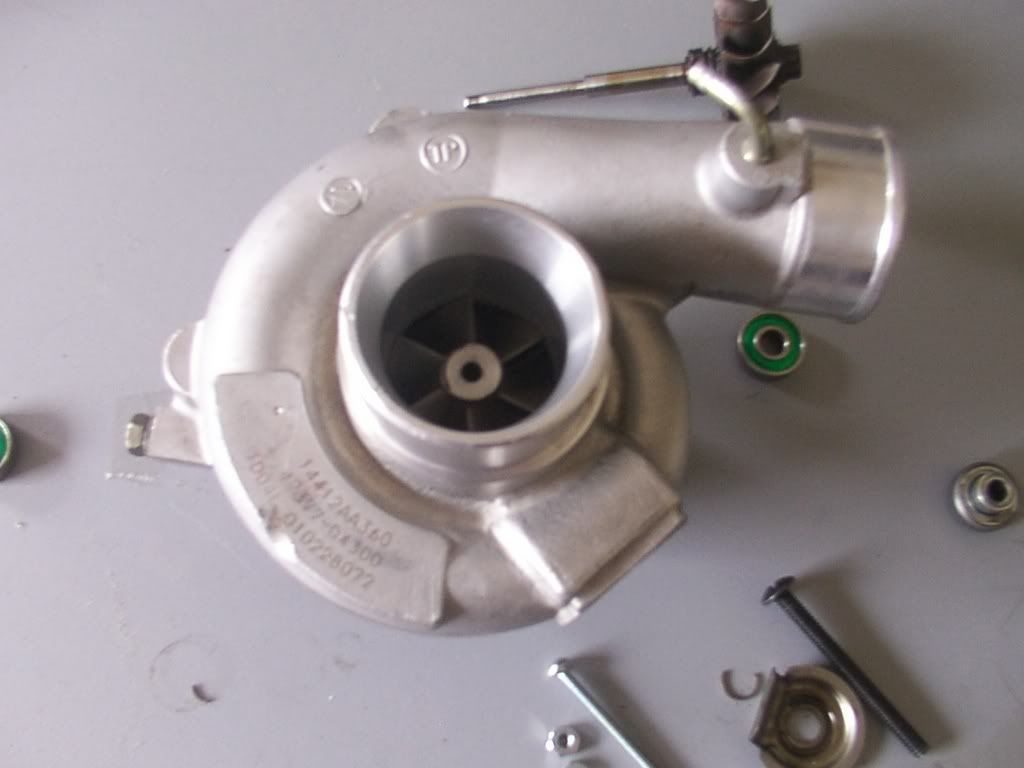
Fabrication has begun and is going well, here is a part of the bracket assembly that will hold the gear/chain/motor assembly onto thr back of the tuebo, basically making it a centrifugal air pump.
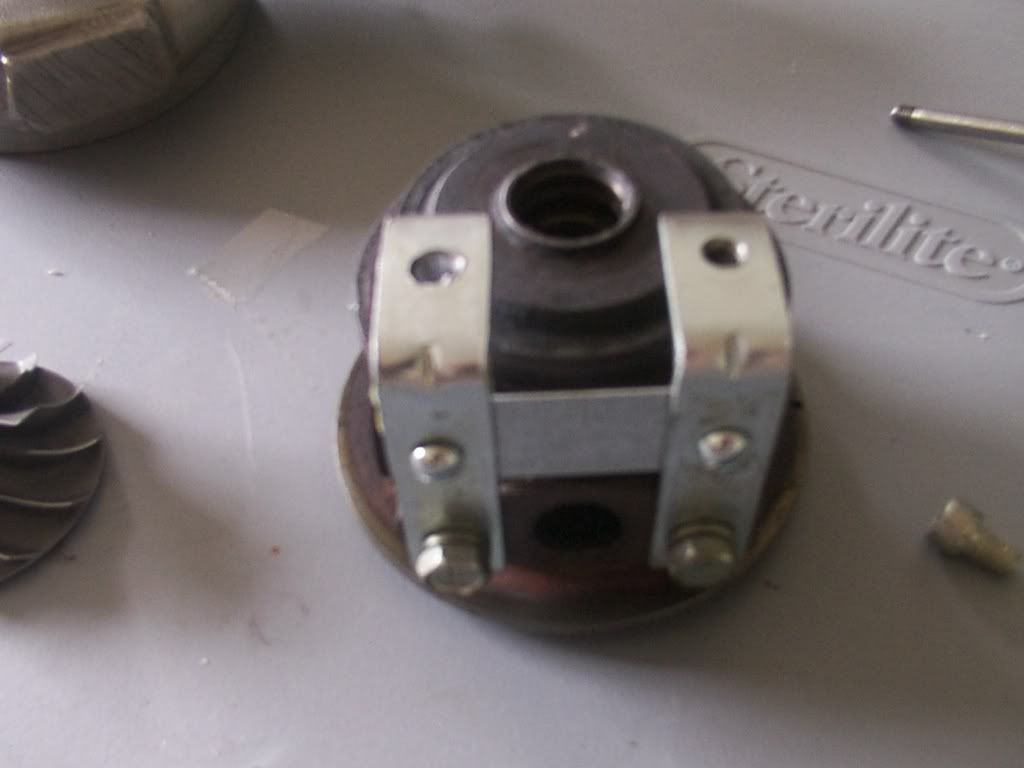
And I'll be off to the machine shop soon to get all the parts I need planned out and machined.
I will, of course, keep everyone updated

*Note* I wasnt entirely truthful about the whole thing as I would have gotten into shit with the moderators on the forum I visit. However, this bastard will work !