Making our own MS terminals
Making our own MS terminals
I know I have talked about this before, but I was just chatting with a member about it, and I think it may be time to push this ahead.
I have a source for tooling to make the mold for MS terminals. I also have a source to inject the plastic. White or black, we pick the color. They would do small production runs, so we can have both colors probably. Also, I took a MS terminal to him and he said the plastic used in it is very cheap. If we made new terminals we would use more modern "space age" plastics which would be virtually indestructible (those were his words).
This would just be the plastic parts. You would supply your current brass parts to put in new plastic shells. Maybe some day we can make new brass, but that is beyond what I am willing to do now.
Who would be interested in these parts? Also, what part is most critical? There are the power terminals, the two pole speaker terminals, and the 4 pole speaker terminals. There are also two styles of the 4 pole and they are not comparable. I personally think the two pole speaker terminals are what is broken the most and what we need to focus on.
The only thing holding me back at this point is a CAD model of a MS terminal.
I have a source for tooling to make the mold for MS terminals. I also have a source to inject the plastic. White or black, we pick the color. They would do small production runs, so we can have both colors probably. Also, I took a MS terminal to him and he said the plastic used in it is very cheap. If we made new terminals we would use more modern "space age" plastics which would be virtually indestructible (those were his words).
This would just be the plastic parts. You would supply your current brass parts to put in new plastic shells. Maybe some day we can make new brass, but that is beyond what I am willing to do now.
Who would be interested in these parts? Also, what part is most critical? There are the power terminals, the two pole speaker terminals, and the 4 pole speaker terminals. There are also two styles of the 4 pole and they are not comparable. I personally think the two pole speaker terminals are what is broken the most and what we need to focus on.
The only thing holding me back at this point is a CAD model of a MS terminal.
Got "schooled" by member shawn k on May 10th, 2011...
No longer really "in tune" with the audio industry, and probably have not been for some time.
Hands down the forum's most ignorant member...
Don't even know what Ohm's law is...
No longer really "in tune" with the audio industry, and probably have not been for some time.
Hands down the forum's most ignorant member...
Don't even know what Ohm's law is...
I´ve been at a few known spots here in austria and showed them what i needed. I ended up with getting quotes for doing the tools only, that kinda blew the roof off my head.
I for sure support the idea you have and would be in to take a few of the off your hands when they are finished. Even tough i need prefer grey ones. I might be able to find a guy that does a CAD drawing for me. But that will take some time.
I think we would have enough with just going with the speaker terminals from the MS2125/MS2250 and their power connector.

I for sure support the idea you have and would be in to take a few of the off your hands when they are finished. Even tough i need prefer grey ones. I might be able to find a guy that does a CAD drawing for me. But that will take some time.
I think we would have enough with just going with the speaker terminals from the MS2125/MS2250 and their power connector.
Music is silver, PHOENIX is GOLD
joerg wrote: Even tough i need prefer grey ones.
Just dye the white one gray
Power and 2 pole speaker terminals I think would be the best place to start with this. Your right that they have the largest calling.
ZX950 X2 1 blk 1 wht
MS1KTA black NIC
MS1KTA white NIB
MS2250TA (x3) 1 in Blue 1 in Red
MS2125TA
MAC200 NIB
MS275 (x2) 1 NIB
MPS2240 NIB
Tantrum 500.2 (x2)
SA1.0 (x2)
ZPA 0.5 X2
ZPA 0.3 X3
Ti DD10 ............
MS1KTA black NIC
MS1KTA white NIB
MS2250TA (x3) 1 in Blue 1 in Red
MS2125TA
MAC200 NIB
MS275 (x2) 1 NIB
MPS2240 NIB
Tantrum 500.2 (x2)
SA1.0 (x2)
ZPA 0.5 X2
ZPA 0.3 X3
Ti DD10 ............
Paging Doctor Jacampb2............................................................. 

Those tender little burgers with them little, itty-bitty grilled onions that just explode in ya mouth like flavor crystals every time you bite into one.. just makes me want to burn this muthafuka down.... Come on, Pookie, let's burn this muthafuka down!!!
What? I was sleeping?FuzzyHoNutz wrote:Paging Doctor Jacampb2.............................................................

Yeah, I can help, I have offered to before when this came up. If someone wants to send me shells, I can do cad drawings. I can also do the brass parts, but the plastic is the most important.
Injection molds are normally HUGE money to have made, are we understanding correctly that this is going to be a low cost/ "calling in some favors" type of job?
LMK, if anyone wants to dontate plastic for a short while, I will do drawings. I believe the ZX/Ti power/ground/rem blocks are already the same and I can do those from ones I have. Would need speaker terminal shells though.
Later,
Jason
M: M100, M44 for a custom amp project
Zx: Zx500, Zx450, Black Zx350
ZxTi: 4 Zx600Ti's, 1 Zx400Ti
Ti: 5 800.1's & 900.7 for a custom amp project. 1 1200.1, 1 1000.2
Tantrum: 2 1200.1's, 1 600.4, 1 500.2
XS: XS6600
Zx: Zx500, Zx450, Black Zx350
ZxTi: 4 Zx600Ti's, 1 Zx400Ti
Ti: 5 800.1's & 900.7 for a custom amp project. 1 1200.1, 1 1000.2
Tantrum: 2 1200.1's, 1 600.4, 1 500.2
XS: XS6600
Well, the issue is I don't need CAD drawings, I need a solid model. Something like an IGS file. My friend would then process this file for shrink, and design a mold for it.
He said it would be far cheaper to make the mold without the holes for the set screws, and then have a jig setup to hand drill them later. This sounded a bit crude to me, but he assured me the parts would be nice even doing this.
The other problem is the power terminal is really quite complex. It has smooth corners and a recessed area around where the wires enter. This styling really looks good if you ask me, and I personally would like to continue the styling to the 2-pole speaker terminals which they never had. The 4-pole terminals on newer amps do have this styling and look great next to the power terminals. These same 4-pole terminals were used on the Bandit and Outlaw amps, although molded in black.
The tooling should be a few thousand at the most. My plan until I lost my job was to get all this done and then whore out the terminals on eBay to cover the costs of the tooling. I really doubt it would ever be a profit maker, but since the quantity of MS terminals in the world is really a fixed number at this point, it is merely a matter of time before all MS owners need them.
Additionally I have found some MS terminals break on their own not from abuse or shipping. The screws were put in with quite a bit of torque at the factory and over time cause some of them to crack off the mounting tab.
He said it would be far cheaper to make the mold without the holes for the set screws, and then have a jig setup to hand drill them later. This sounded a bit crude to me, but he assured me the parts would be nice even doing this.
The other problem is the power terminal is really quite complex. It has smooth corners and a recessed area around where the wires enter. This styling really looks good if you ask me, and I personally would like to continue the styling to the 2-pole speaker terminals which they never had. The 4-pole terminals on newer amps do have this styling and look great next to the power terminals. These same 4-pole terminals were used on the Bandit and Outlaw amps, although molded in black.
The tooling should be a few thousand at the most. My plan until I lost my job was to get all this done and then whore out the terminals on eBay to cover the costs of the tooling. I really doubt it would ever be a profit maker, but since the quantity of MS terminals in the world is really a fixed number at this point, it is merely a matter of time before all MS owners need them.
Additionally I have found some MS terminals break on their own not from abuse or shipping. The screws were put in with quite a bit of torque at the factory and over time cause some of them to crack off the mounting tab.
Got "schooled" by member shawn k on May 10th, 2011...
No longer really "in tune" with the audio industry, and probably have not been for some time.
Hands down the forum's most ignorant member...
Don't even know what Ohm's law is...
No longer really "in tune" with the audio industry, and probably have not been for some time.
Hands down the forum's most ignorant member...
Don't even know what Ohm's law is...
"build a 3D scanner", are you planning to build your own? That would be a hell of an undertaking!
I have all the terminal styles I am talking about and could probably send them too you. What format would your final model be exported as?
I have all the terminal styles I am talking about and could probably send them too you. What format would your final model be exported as?
Got "schooled" by member shawn k on May 10th, 2011...
No longer really "in tune" with the audio industry, and probably have not been for some time.
Hands down the forum's most ignorant member...
Don't even know what Ohm's law is...
No longer really "in tune" with the audio industry, and probably have not been for some time.
Hands down the forum's most ignorant member...
Don't even know what Ohm's law is...
I can make it to almost any type of file. 3dm, 3ds, ai, obj, stl, iges, raw...You name it and I can export it for you.
As far as building a 3d scanner, it has actually become quite simple. There are several programs that use standard lasers to build from. After I get that done, Ill need an excuse to start on this:
As far as building a 3d scanner, it has actually become quite simple. There are several programs that use standard lasers to build from. After I get that done, Ill need an excuse to start on this:
- Attachments
-
- P1013517.jpg (110.04 KiB) Viewed 11851 times
The brass parts slide into the plastic parts and are loose. The set screws for the connections actually also retain the brass into the plastic.
Got "schooled" by member shawn k on May 10th, 2011...
No longer really "in tune" with the audio industry, and probably have not been for some time.
Hands down the forum's most ignorant member...
Don't even know what Ohm's law is...
No longer really "in tune" with the audio industry, and probably have not been for some time.
Hands down the forum's most ignorant member...
Don't even know what Ohm's law is...
I have enough white terminals at last. But it's always worth having spares for the future "just in case" situations.
Maybe if everyone on PP chipped in $50 to $100 (or whatever they wanted) in advance, then divide up the stash of 1000's of units accordingly later. That way no one person has to pay a huge bill. Just a thought.
Or you could just sell them off individually on ebay. Put them on a nice rug, advertised as limited editions, never to be repeated
(I can only help drawing things in 2D, like logo's etc in Freehand / Illustrator, so no use here!)
Maybe if everyone on PP chipped in $50 to $100 (or whatever they wanted) in advance, then divide up the stash of 1000's of units accordingly later. That way no one person has to pay a huge bill. Just a thought.
Or you could just sell them off individually on ebay. Put them on a nice rug, advertised as limited editions, never to be repeated

(I can only help drawing things in 2D, like logo's etc in Freehand / Illustrator, so no use here!)
Machining them is not a bad idea, but I doubt it would be all that much cheaper, and I am concerned the parts would not be the same quality (looks).
Besides, once the tooling is made to mold them, I will keep it. If 10 years from now someone needs terminals, they can be molded again at that time. Due to the small numbers, the tooling will likely never wear out.
Putting them on a rug and dumping them on eBay is not a bad idea, and it would clearly stir the pot of those eBay "high rollers" you are referring to.
Besides, once the tooling is made to mold them, I will keep it. If 10 years from now someone needs terminals, they can be molded again at that time. Due to the small numbers, the tooling will likely never wear out.
Putting them on a rug and dumping them on eBay is not a bad idea, and it would clearly stir the pot of those eBay "high rollers" you are referring to.
Got "schooled" by member shawn k on May 10th, 2011...
No longer really "in tune" with the audio industry, and probably have not been for some time.
Hands down the forum's most ignorant member...
Don't even know what Ohm's law is...
No longer really "in tune" with the audio industry, and probably have not been for some time.
Hands down the forum's most ignorant member...
Don't even know what Ohm's law is...
- nico boom
- Deus ex MS
- Posts: 2089
- Joined: Fri Jan 05, 2007 1:40 pm
- Location: the land of wooden shoes
I have undertaken several attempts in the past ,to have those connectors made.
Closest solution was to machine the plastic housings, and fit them with round [not square] brass inserts.
After gold-plating the new inserts, the price was simply too high to give the go-ahead on this.
I think the original brass inserts will be usable in most cases, so only the plastic housings need to be injection-molded some way or another.
Since these housings are only used on the MS and MPS series, what numbers are we actually talking about..?
I will ask a new local company that does injection molding about it next week; one never knows....
In the mean time good luck working on this guys.
Closest solution was to machine the plastic housings, and fit them with round [not square] brass inserts.
After gold-plating the new inserts, the price was simply too high to give the go-ahead on this.
I think the original brass inserts will be usable in most cases, so only the plastic housings need to be injection-molded some way or another.
Since these housings are only used on the MS and MPS series, what numbers are we actually talking about..?
I will ask a new local company that does injection molding about it next week; one never knows....
In the mean time good luck working on this guys.
The tooling is likely the expensive part. And since a friend of mine owns a shop making this tooling, he is willing to cut me a deal to do it.
I plan to make them and sell them on eBay to pay off the tooling over time.
I plan to make them and sell them on eBay to pay off the tooling over time.
Got "schooled" by member shawn k on May 10th, 2011...
No longer really "in tune" with the audio industry, and probably have not been for some time.
Hands down the forum's most ignorant member...
Don't even know what Ohm's law is...
No longer really "in tune" with the audio industry, and probably have not been for some time.
Hands down the forum's most ignorant member...
Don't even know what Ohm's law is...
- nico boom
- Deus ex MS
- Posts: 2089
- Joined: Fri Jan 05, 2007 1:40 pm
- Location: the land of wooden shoes
From an economical point of view that will be the only way to make it work Eric; hope it will happen so!Eric D wrote:The tooling is likely the expensive part. And since a friend of mine owns a shop making this tooling, he is willing to cut me a deal to do it.
I plan to make them and sell them on eBay to pay off the tooling over time.

- mhyde71
- Dr. Jekyll
- Posts: 6231
- Joined: Sun Jan 20, 2008 8:34 pm
- Location: PG FanBoy in Green Mtn Vermont
- Contact:
there is also a process called SLS (think thats what it is called anyways) AND when i was looking into it a local company to me offered to do a batch of 100 using the SLS process (which requires little to no tooling- don't know the specifics...) but when dealing with lower numbers of like under 500 the SLS process would be the way to go- but over that amount the most efficient/economic way is to have the tooling made up...
Funny thing is when i was poking around with the idea... i actually got in touch with the exact same company in Taiwan that made them back in the day for PG- Thought i was on to something when I spoke to the rep that handles it for PG in Taiwan and he said (at first) sure how many do you need....when it got down to it, he realized/learned that the tooling had been junked- prolly maxed out and sold for scrap or tossed in alley somewhere then sold for scrap from one of the country Chinese people.
Lucky for me that my wife is Chinese and was able to speak to him directly and clearly (i mean he did speak English) but well we know ho that goes. - BUT it was a major let down-
thought for sure I was onto something there when i was able to find out who made them... BUT the quote for the tooling to do again was to the likes of 7500/10K -
Funny thing is when i was poking around with the idea... i actually got in touch with the exact same company in Taiwan that made them back in the day for PG- Thought i was on to something when I spoke to the rep that handles it for PG in Taiwan and he said (at first) sure how many do you need....when it got down to it, he realized/learned that the tooling had been junked- prolly maxed out and sold for scrap or tossed in alley somewhere then sold for scrap from one of the country Chinese people.
Lucky for me that my wife is Chinese and was able to speak to him directly and clearly (i mean he did speak English) but well we know ho that goes. - BUT it was a major let down-
thought for sure I was onto something there when i was able to find out who made them... BUT the quote for the tooling to do again was to the likes of 7500/10K -
PAST WORK/S HERE::
https://www.facebook.com/KhameleonKoatings/photos_albums
https://www.facebook.com/KhameleonKoatings/photos_albums
- mhyde71
- Dr. Jekyll
- Posts: 6231
- Joined: Sun Jan 20, 2008 8:34 pm
- Location: PG FanBoy in Green Mtn Vermont
- Contact:
AND to add to what Nico was saying about having the centers made to be round... same thing i heard from another local fab shop- they said the square cut outs would have to broached and then it is still difficult b/c of the flange at one end - or thats why it would have to be broached- BUT this is going by or using even a different process... They said they would make a couple prototypes for me at cost and was looking at 150 for a pair of them.
Never pursued it after that
ended up just getting a couple TA's off the bay and using those connectors for the MS1K instead. fixing the broken ones and selling off the TA's for a lil loss, but got out of it for about the same money i think....and they were OEM.
I have a couple extra connectors Eric if you need some for samples- BUT I WOULD NEED BACK whenever it is possible.
I have power and speaker term's I could pony up for however long you need them for whatever your into doing...?!
Never pursued it after that

ended up just getting a couple TA's off the bay and using those connectors for the MS1K instead. fixing the broken ones and selling off the TA's for a lil loss, but got out of it for about the same money i think....and they were OEM.
I have a couple extra connectors Eric if you need some for samples- BUT I WOULD NEED BACK whenever it is possible.
I have power and speaker term's I could pony up for however long you need them for whatever your into doing...?!
PAST WORK/S HERE::
https://www.facebook.com/KhameleonKoatings/photos_albums
https://www.facebook.com/KhameleonKoatings/photos_albums
selective laser sintering.. its a rapid prototyping technique.. spread a layer of powder onto a table, use a laser to solidify the section you want to keep, drop the table down a few thousandths, spread more powder.. rinse and repeat. not sure how well it applies to these, but the machines typically have a large table, since the laser doesnt have to travel much (just rotates on 2 axis) so somebody could fit a ton of these on it.mhyde71 wrote:there is also a process called SLS (think thats what it is called anyways) AND when i was looking into it a local company to me offered to do a batch of 100 using the SLS process (which requires little to no tooling- don't know the specifics...) but when dealing with lower numbers of like under 500 the SLS process would be the way to go- but over that amount the most efficient/economic way is to have the tooling made up...
Funny thing is when i was poking around with the idea... i actually got in touch with the exact same company in Taiwan that made them back in the day for PG- Thought i was on to something when I spoke to the rep that handles it for PG in Taiwan and he said (at first) sure how many do you need....when it got down to it, he realized/learned that the tooling had been junked- prolly maxed out and sold for scrap or tossed in alley somewhere then sold for scrap from one of the country Chinese people.
Lucky for me that my wife is Chinese and was able to speak to him directly and clearly (i mean he did speak English) but well we know ho that goes. - BUT it was a major let down-
thought for sure I was onto something there when i was able to find out who made them... BUT the quote for the tooling to do again was to the likes of 7500/10K -
I think it usually ends up with a result similar to modern stereolithography, which is a brittle part that's great for checking fit, but not really usable. I'm not intimately familiar with it though.
also, i'm fairly certain theres enough room there to machine the corners out to allow for the original inserts to be used, but my opinion may change if I had one infront of me.
I'm afraid of widths.
The MS power terminals are the same as the ZX/Ti terminals (on the newer MS amps that is).
I have all the terminals I need, I just need to make CAD models of them. I would get around to it, but I have been kind of busy with the holidays.
I have all the terminals I need, I just need to make CAD models of them. I would get around to it, but I have been kind of busy with the holidays.
Got "schooled" by member shawn k on May 10th, 2011...
No longer really "in tune" with the audio industry, and probably have not been for some time.
Hands down the forum's most ignorant member...
Don't even know what Ohm's law is...
No longer really "in tune" with the audio industry, and probably have not been for some time.
Hands down the forum's most ignorant member...
Don't even know what Ohm's law is...
actually if you get a mould made of brass it's not so time consuming to make (all is relative) thats how we make prortotype moulds if the designers need to see how the ejection and other potential problems work - and it can make enough teminals to last a lifetime if it doesn't have to be polycarbonate - i think abs plastic would do ok
Kenwood DDX5016DAB
In stock awaiting install ideas
Alpine 7893R
PG Rsd 65cs
2 PG M100
2 12" Xmax
PG Bass Cube Special Edition
PG Xmax 10"
Old School CVIT15.0DVC
PG M50
PG M44
PG M25 Special Edition
PG Xenon 6,5"
PG TiDD10 + Sld44
PG ZX 475TI (Needs check, bought as blown)
In stock awaiting install ideas
Alpine 7893R
PG Rsd 65cs
2 PG M100
2 12" Xmax
PG Bass Cube Special Edition
PG Xmax 10"
Old School CVIT15.0DVC
PG M50
PG M44
PG M25 Special Edition
PG Xenon 6,5"
PG TiDD10 + Sld44
PG ZX 475TI (Needs check, bought as blown)
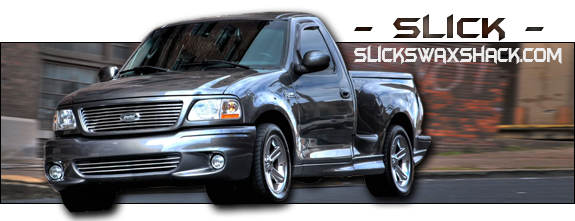
Our Rides :
2008 Ford EdGe Limited , Blazin Copper
2004 Ford SVT Lightning , Dark Shadow Grey 5.4L Eaton Supercharged . Powered By Memphis .
2003 Dodge Ram - Stock Stereo , Added Memphis sub and Amp
1997 Dodge Ram - Kenwood / Soundstream / Eclipse / Memphis / Rockford Fosgate / PG
My PG collection : For Sale.