This is just one example but the idea is useful for any kind of fabricating. Whether it is flat wood panels or contoured fiberglass pieces.
In this example I was making trim panels fan out from the amps and butt-up to the factory side panels. The side panels had crazy contours where they were to meet and trying to cut to wood exactly to shape would've been tough to say the least. The piece your are working with does not need to be cut perfectly to shape. Just close.
Tape-off the piece you are trying to match around the area the two pieces meet. Put your trim panel back in place. Using bondo, fill the gaps between the pieces and let harden. The bondo will not stick to the tape but will stick to anything not taped. So be careful to protect anything else that might be at risk.
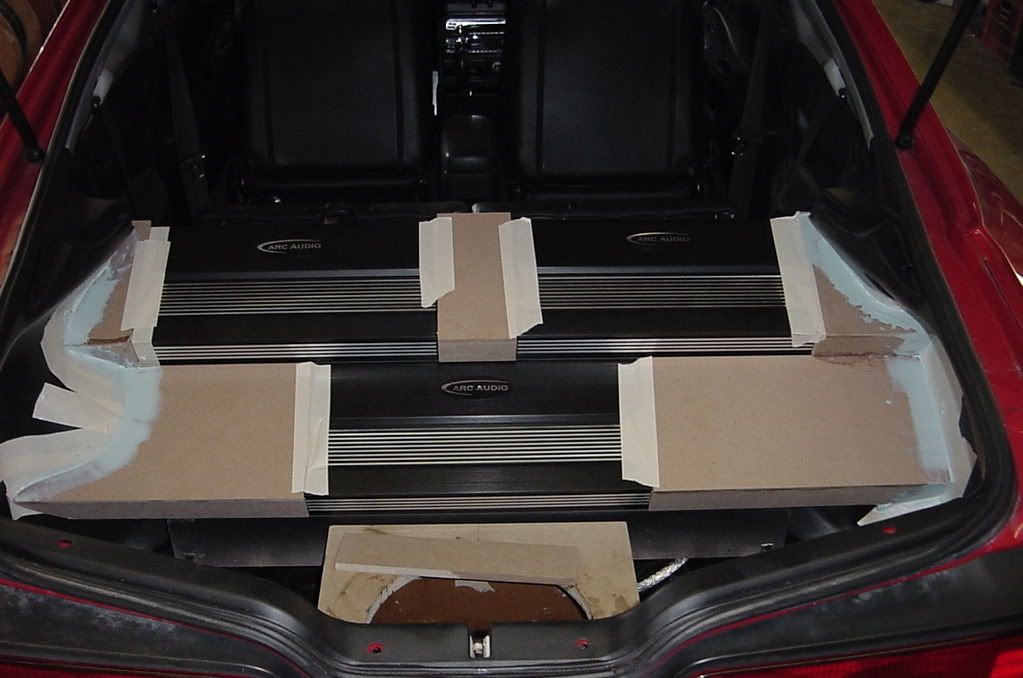
Obviously, the closer your 'guess' is on the original cut, the less bondo you will need. Also, if your gaps are large, the bondo will have the tendency to fall out before hardening. No problem. Just use tape on the back side of your work to form a bridge between the pieces. Helping keep the bondo in place till it hardens.
Once it has hardened, pull out your piece, sand the surface smooth and viola, a perfect fit.
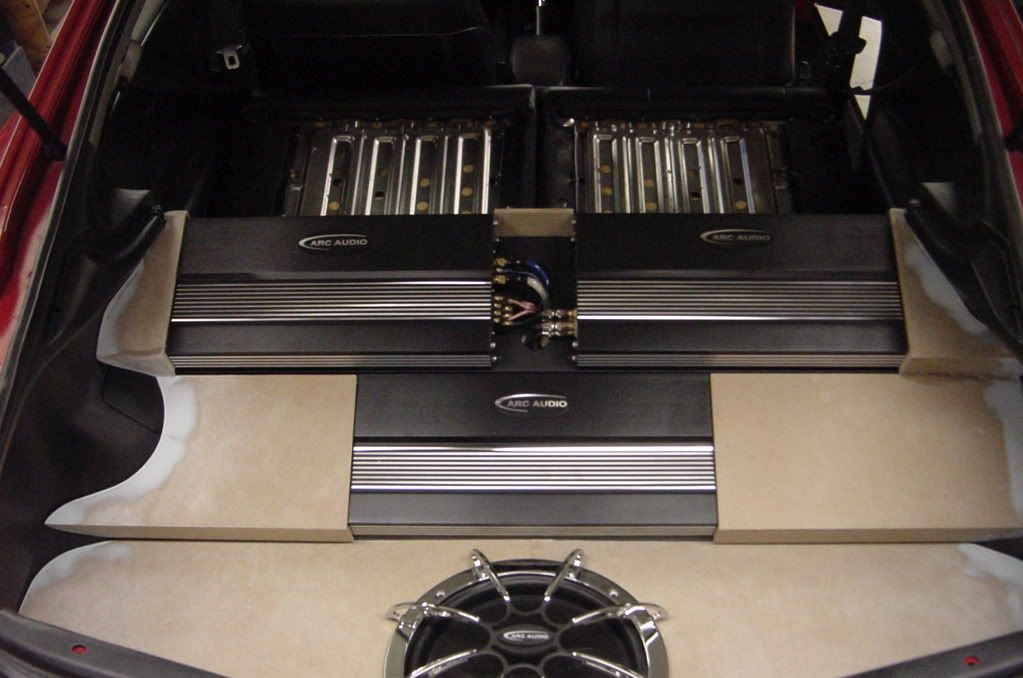
One other thing to consider is the thickness of the material you are gonna rap the finished product in. In this case vinyl was used and the piece it butted-up to had some 'give' to it so I didn't need to worry about thickness. But if that's not the case then you can layer the tape on the piece you're matching to accomidate the thichness of the material you're rapping with
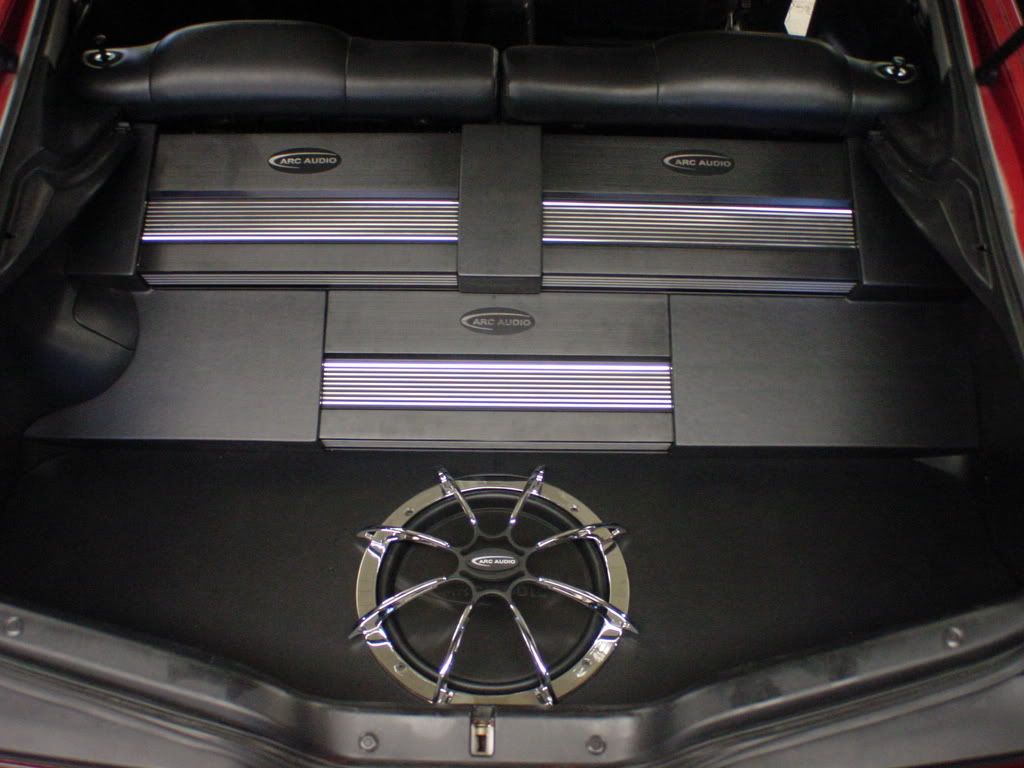
One other tip. Cutting grooves in the end of your trim that is to be filled-in will help the bondo to adhere better. Also, while bondo works fine for most applications, duraglass is often perfered for it's strength over bondo.
The pics are kinda self explanatory but if I left anything out just ask. I will elaborate.